COOL ROOF MATERIALS
FOAM (SPF)
Installing Sprayed Polyurethane Foam roofing system on a new building, or retrofitting your older roof with an SPF roof can save you money in a lot of different ways. Most of the causes of additional roofing expenses don’t exist when you have a foam roof system. Foam Roofs have no seams to split or pull apart and allow water to enter. Foam is ideal for saw tooth or other irregular roof shapes that are difficult or impractical for old fashioned low-tech roofing materials. Sprayed Polyurethane Foam is also the best insulator on the market. Very little maintenance or repair is ever needed, and with proper care, it is the last roof you will ever need to buy.
BENEFITS & SAVINGS
Closed cell Polyurethane Foam roofing keeps your roof carefree for years to come. The light weight of a foam roof offers very little increase in load on your existing structure, while providing a self-flashing, seamless blanket of protection. The low historical leakage rate of foam roofing systems also means fewer headaches when the weather outside turns bad. The low heat conductivity of foam can also cool down your summer air conditioning bills. Rain or shine, foam roofing is about weather and energy solutions not more problems, and what business couldn’t use that?
The “renewable” quality of foam roofing is a real money saver. When most other roofs are destined for the landfill, your roof is not. As long as the foam layer of your roof is protected with the ultraviolet resistant top coat, your foam roof remains as good as the day it was installed.
Foam roofing has many advantages over traditional roofing methods.
- Seamless: Polyurethane foam is applied as a liquid, creating a single monolithic membrane that covers the entire roof. There are no seams or joints, the source of the majority of leaks in traditional roofs.
- Flexible: The foam can be sprayed onto virtually any surface, irregularly shaped roofs and protrusions are readily taken care of.
- Lightweight: Foam roofing typically weighs around 50 lbs. per square, versus 800 lbs. for a built-up roof and 100 lbs. for ballasted single-ply roofs.
- Thermal Insulation: SPF has the best insulating properties available for commercial construction today.
- Sustainability: Foamed roofs require a minimum of upkeep, creating little waste and have an indefinite lifespan.
DENSITY & R-VALUE
Density of SPF is important when it comes to strength and Thermal Resistance. Obviously, higher density means increased strength and higher R-value. Most SPF roofs have densities ranging from about 2.5 pounds per cubic foot to 3 pounds per cubic foot. Three pound density foam has a compressive strength of about 50 psi and an R-value of 7.14 installed and 6.86 aged (these numbers may vary slightly depending on the foam manufacturer. Here’s an example of how well a good SPF roof insulates. A school district in southern California had recently installed some new, one-room relocatable classroom buildings. During the late spring and early fall, these classrooms were using their air conditioners an average of 50 minutes every hour. The school district installed foam roofs on some of these classrooms in order to see if it would provide an energy savings. The roofs consisted of three pound density foam, 1.5 inches thick with an acrylic coating system. The air conditioner usage was cut down to fifteen minutes every hour. That’s a fifty-eight percent savings on energy costs.
WHAT IS SPRAYED POLYURETHANE FOAM
Sprayed Polyurethane Foam is a combination of isocyanate and polyol. These two components are fed through a proportioner which heats then pumps the two separate components to the spray gun, where they are mixed and sprayed onto the substrate. Because it is sprayed onto the roof as a liquid, it forms a single continuous structure that is seamless and very stable. SPF requires a clean surface for proper application. It must be dry, free of contaminants like oil, and properly fastened to the substrate in accordance with the proper building codes. A protective elastomeric top coat is required which is typically sprayed on as well, but it is also possible to be applied with hand or power rollers.
SPF’S WATERPROOFING ABILITIES
Sprayed Polyurethane Foam is perfect for many different waterproofing applications. Because it is composed of billions of closed cells, the foam acts as an air barrier, preventing moisture infiltration into the building. This ability minimizes dew point problems, which unchecked lead to water condensation inside of the structure. Moisture infiltration into the building envelope is the number one cause of building deterioration.
Even when the top coat of a foam roofing system is damaged, the underlying foam will keep the roof from leaking. The Superdome in New Orleans was damaged once in a severe hail storm. Thousands of hairline cracks appeared in the top coat, but no leaks ever occurred, even though it wasn’t repaired for over a decade!
If a penetration does occur all the way from the foam layers, the water infiltration will be isolated only to the area where the membrane has been penetrated. Small penetrations in foam roofing systems can be repaired easily with an elastomeric caulk, reinstating the integrity of the system.
Water ponding is quite often a problem with conventional roofing systems. When applying the polyurethane foam in reroofing situations, it is very easy to build up areas of greater thickness while spraying so that water will drain properly. This also eliminates the problem of the additional weight load associated with water accumulation.
METAL
Metal roofs are durable, fire retardant and almost maintenance-free. They reflect heat and block its transfer into the building’s top floor. Research by the Florida Solar Energy Center in 1985 showed that metal absorbed 34% less heat than asphalt shingles.
TILE
Roofing Tiles can be ceramic or fabricated from cement concrete. Some of the lighter-weight types contain fibers (e.g., cellulose) for added strength. The color of a tile may be applied as a coating or dispersed throughout. Perhaps the most common type of roof tile is the Spanish-style red barrel tile made from fired clay.
The modern version of this tile is sometimes a cement tile with a suitable coating. They can have respectable reflectance ratings if they are of a light color. They also have enhanced air circulation compared to other roofing types, because ambient air can circulate below as well as above the tile. Enhanced air circulation helps the roof shed solar heat more readily. Solar reflectance levels for tiles range from a low of 0.18 for red concrete tile to a high of 0.74 for white concrete tile. Tile is more appropriate for steeper-sloping roofs.
RUBBER
Due to inflexibilty, weathering, and joints that fail, sooner or later flat roofing methods will end up leaking. If you have been dealing with a flat roof leak, you will be happy to know that rubber roofing materials will eliminate all leaks. Rubber roofing provides many years of leak free service.
WHY RUBBER ROOFING?
- Durability and Low Maintenance
- Class A Fire Rating
- High Value to Homeowner
- Environmentally Friendly and Recyclable
- Favorable by Insurance Industry
- Excellent Insulator in Very Hot or Cold Temperatures
ASPHALT
Asphalt shingles come in two basic types: glass fiber (a.k.a. fiber glass) and organic. Organic shingles consist of an organic felt material which is generally paper saturated with asphalt to make it waterproof. A top coating of adhesive asphalt is then applied and the ceramic granules are then embedded. Organic shingles contain around 40% more asphalt per square (100 sq. ft.) than their glass fiber counterpart which makes them weigh more and gives them excellent durability and blow-off resistance.
Glass fiber shingles have a glass fiber reinforcing mat manufactured to the shape of the shingle. This mat is then coated with asphalt which contains mineral fillers. The glass fiber mat is not waterproof by itself. It’s purpose is for reinforcement. What makes the glass fiber shingle waterproof is the asphalt. However, the asphalt itself will not stick to the mat. For this reason, “fillers” are used. The fillers in the asphalt cling to the glass fibers in the mat. The asphalt then encapsulates the glass fibers, fills all of the little holes and voids in the mat rendering it waterproof. After this cools a bit, an adhesive asphalt is used to cover the mat and the ceramic granules are then embedded.
SO WHICH TYPE IS BETTER?
By far, the more popular shingles are the glass fiber ones. This may be attributed to the fact that they are cheaper and easier to manufacturer than organic shingles making them more cost effective to the homeowner, or it may be that they are easier to work with, or they may simply be a personal preference of the roofing contractor.
(click image to enlarge)
HOW LONG DO THEY LAST?
The lifespan of asphalt shingles depends highly upon the environment. Shingles in cooler climates such as the northern United States seem to last longer than those installed in the warmer climates. Studies have shown that the average lifespan for a 20 year shingle in Phoenix, Arizona is around 14 years. In Minneapolis, Minnesota the lifespan was 19.5 years. And in Reading, Pennsylvania, the lifespan was 20.8 years. From this data it seems obvious that the hotter the environment is, the shorter the service life of the shingles. One thing that’s very damaging to shingles is Thermal Shock. Thermal Shock is what roofing materials experience when the ambient temperature changes dramatically within a very short period of time – usually 24 hours. For example, in Yreka, California, the temperatures during a summer day can often reach 100 degrees and at night, they’ll often drop below 50, sometimes as low as 40. Roofing materials are unable to expand and contract to accommodate such a dramatic temperature change in such a short period of time so cracks and splits in the materials start occurring. Water can then enter the materials and damage them further in two ways. One is the damage water does to asphalt materials in general. It’s not that water hurts asphalt, but algae and fungus do and the continuous presence of water will permit algae and fungus to grow on asphalt materials. Another way water damages is the freeze-thaw cycle. In the cold months, water will get into the cracks and then freeze at night. Water expands as it freezes so the more this occurs, the bigger the cracks or splits become. This is why most roofing contractors and consultants are such big advocates of sloped roofs. The better the roof sheds water, the less problems it will usually experience.
Still another factor affecting asphalt shingle roofs is attic ventilation. Proper roof ventilation has been known to extend the service life of a roof. Whether it is because it has a direct effect on the shingle themselves or on the other components such as the roof deck is uncertain.
FOAM
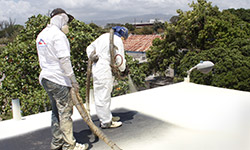
METAL
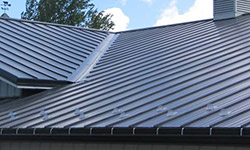
TILE
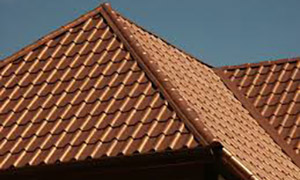
RUBBER
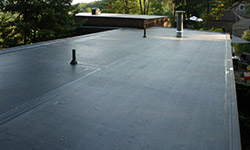
ASPHALT
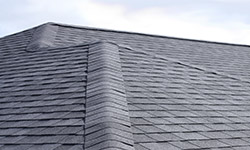
Green Team Roofing
Residential and Commercial Roofing Solutions
A Green Company – Licensed, Bonded & Insured
Only takes a few seconds!